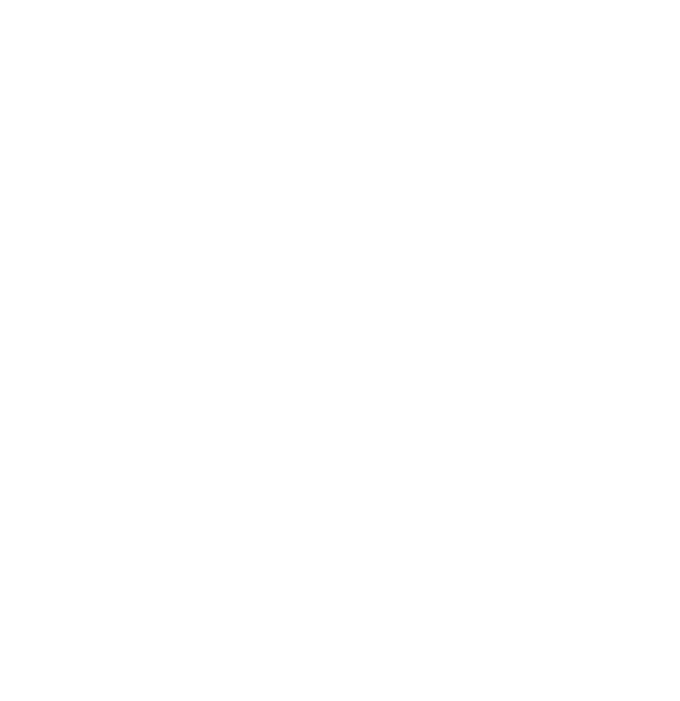
Safety Leadership Training for Line Management
Training
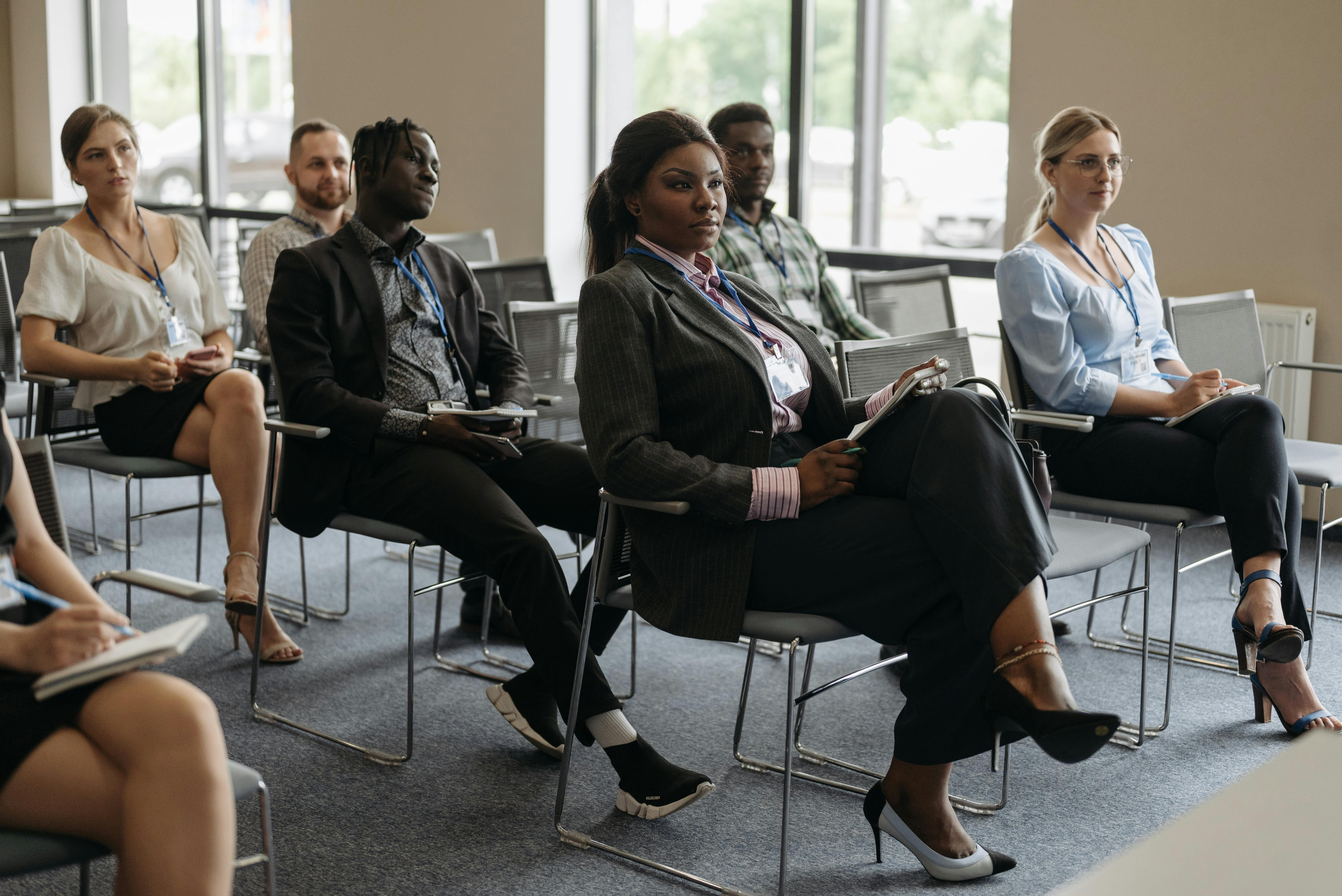
“Toxic Leadership” is a combination of self-attitudes, motivations and behavior that have adverse effects on subordinates, the organization and mission performance. This Leader lacks concern for others and the climate of organization, which leads to short and long negative effects” (Leadership development, 2015) At every organizations, safety programs will fails following toxic leadership and commitments in particular at line management level. Line management inspire employees on what is expected of the attaining and sustaining the safety acts.
About the Training
- Duration: 16 hours
- Target Audience: Supervisors, Superintendents, Foremen, Group Leaders
- Objective: To empower line managers to lead and sustain safety practices within their teams.
Training Modules
Part 01 - Understanding Incident Causation Model
Safety is about preventing accidents and incidents in the workplace. Accident and incident prevention programs will succeed if implemented with proper and sufficient processes. Each workplace has specific potential risks depending on the nature of its processes, and sufficient risk management programs are key to preventing workplace accidents. Participants will learn the contributing factors leading to accidents and incidents and how to correct them.
Part 02 - Communicating Personal Safety Commitment
Being a leader means inspiring others. Line management should initiate processes to drive safety programs within their working groups. Line management plays an essential role in developing the vision and mission for safety, which is reflected in individual actions and decisions regarding safety matters. "Production vs. safety" is a common dilemma among leaders, and line management should be able to prioritize safety on par with production.
Part 03 - Leadership Role in Safety
Being a leader means inspiring others, including subordinates and peers. Leaders must initiate systems and processes to ensure safety programs are effectively implemented in their areas of responsibility. Four leadership attitudes and behaviors can create barriers to the development of safety programs:
- Inconsistency
- Obsolete rules and procedures
- Us vs. Them mentality
- Leadership deficiency
Part 04 - Individual Safety KPI
By establishing specific goals and objectives, management sets expectations for managers, supervisors, and workers, and for the program overall. The goals and objectives should focus on specific actions that will improve workplace safety and health. Line management will learn how to set SMART safety programs.
Part 05 - Breaking Up the “SILO” Mentality
What is a Silo? It is a mindset present when certain individuals, departments, or sectors do not wish to share information with others in the same department, function, or organization. This mentality reduces overall operational efficiency, lowers morale, and can contribute to the demise of a productive company culture. Participants will learn how to break up this “SILO” mentality and encourage teamwork to implement safety programs effectively.
Part 06 - Running Safety Committee Meetings
A safety committee is the best place to communicate and evaluate safety programs and gain maximum feedback from employees. Safety committees should be developed from representatives of management and employees. Participants will learn how to develop and run effective safety committees.
Part 07 - Implementing Behavior-Based Safety Observation
Unsafe acts are a major cause of workplace accidents and incidents (85%). Through effective behavior-based safety observation (STOP) programs, all employees and line management are encouraged to participate in preventing workplace accidents and incidents. Participants will learn how to develop and implement effective behavior-based safety observation programs.
Part 08 - Implementing Workplace Safety Inspection
Workplace hazards will always be present as long as activities, materials, processes, etc., are performed in the workplace. Physical, biological, chemical, and energy hazards can be eliminated at their sources by implementing effective workplace safety inspections on a regular basis. Participants will learn how to develop workplace inspection checklists, implement regular workplace safety inspections, and monitor corrective actions.
Part 09 - Implementing Toolbox Meetings
Error is a human factor by nature, and toolbox meetings are aimed at reminding everyone of today’s hazards and how to prevent them. Each leader should have the ability to communicate safety issues in the workplace. Participants will learn how to conduct toolbox meetings on a daily basis.
Part 10 - Implementing Job Safety Analysis (JSA) & HIRA DC
Job Safety Analysis (JSA) and Hazard Identification Risk Assessment & Determining Control (HIRA DC) are tools used to map potential hazards in the workplace and/or during activities. Developing the JSA and HIRA DC documents will help local management and employees mitigate any risks arising from day-to-day activities. Participants will learn how to develop JSA and HIRA DC, including mitigation actions.
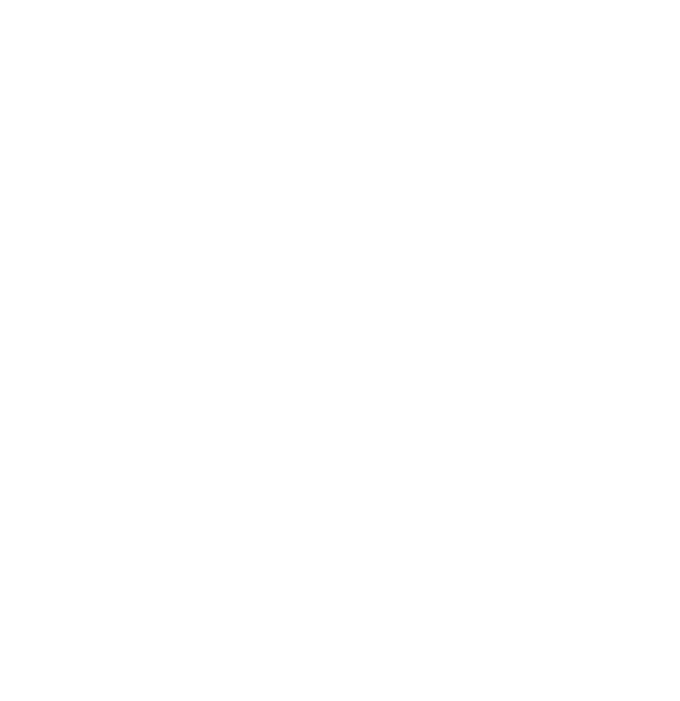
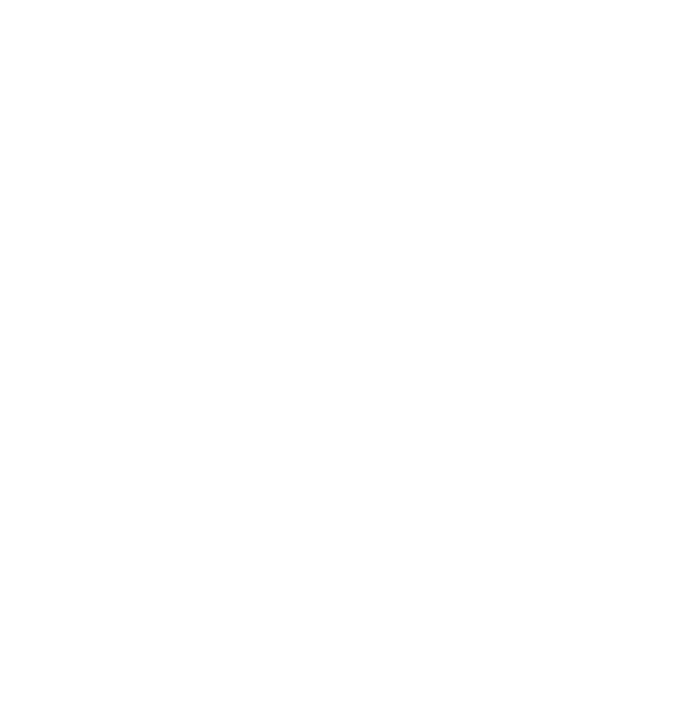
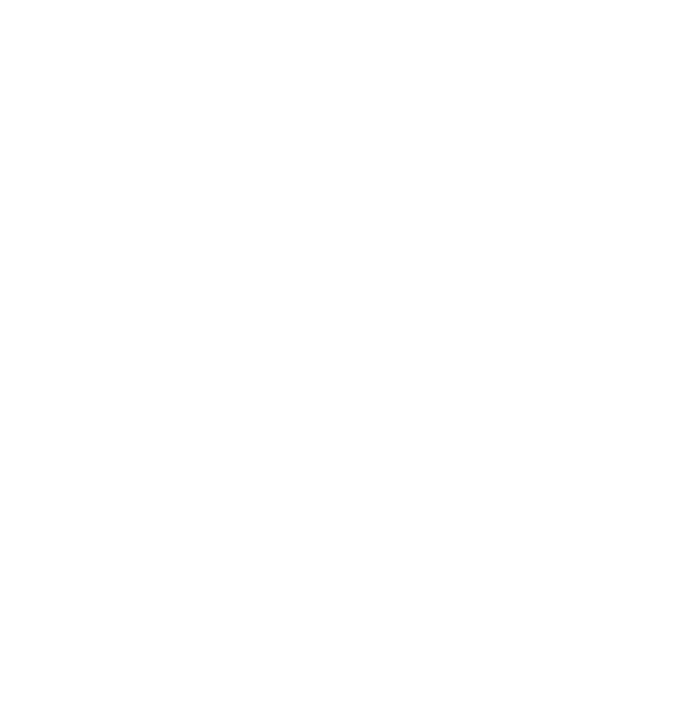
Ready to Talk?
Schedule a call or follow us on social media, stay in touch.
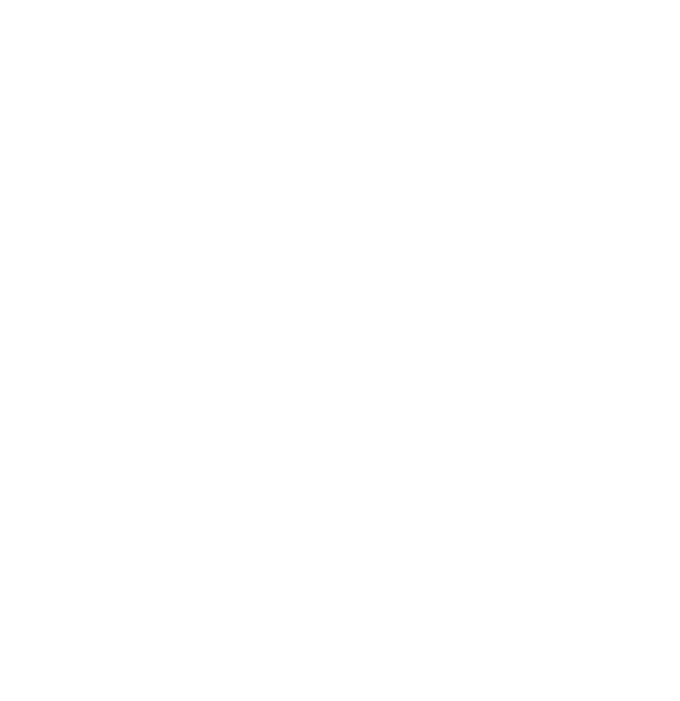